машина по выпуску фанеры, Производственная линия по выпуску фанеры, Оборудование по выпуску фанеры
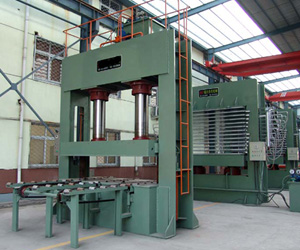
В процессе производства, а именно при резке сырья (бревно), расслаивании, сушке, обработке, горячем прессовании, обрезке краев, полировке происходят отходы лесоматериалов. Отходами являются остатки обработки (Видимый) и сжатия (Невидимый). Отходы лесоматериалов тесно связаны с материалом, спецификацией бревна, производительностью оборудования, технологией и спецификацией продукции.
1) Резка бревна
Как правило, импортное бревно обладает длиной более 6 метров. Бревно должно нарезано в соответствии с длиной и качеством продукции. Длина резки должна быть суммой длины продукции и длины остатков. Например, продукт обладает длиной 1220мм или 2440мм. Длина реза обычно 2600м или 1300 мм. Длина, погибь и дефекты бревна окажут прямое воздействие на окончательный выход фанеры. Отходы включают в себя кусочки дерева, остатки, древесные опилки и т.д. Обычно коэффициент потери бревна составляет 3% - 10%
2) Резка
Резка является самым популярным процессом для производства фанеры. Оборотная стороны фанеры обладает толщиной примерно 0.6 мм, а сердцевина фанеры -1.8 мм.
3) Сушка
Шпон является влажным после резки. Он дожжен быть высушен в соответствии с технологическими требованиями. После сушки, длина, ширина и толщина шпона уменьшается. Потеря связана с материалом, влажностью и толщиной шпона. Коэффициент потери обычно составляет 4%-10%.
4) Обработка
Обработка включает в себя резку, соединение фанеры и исправление фанеры. Ленточные шпоны нарезаны на шпоны с подходящим размером или соединимые шпоны. Узкие ленточные шпоны могут быть соединены в целый шпон. Дефектные шпоны становятся качественными шпонами путем исправления. Отходы на данном этапе связаны с используемым материалом бревна, качеством резки, качеством сушки и квалификацией рабочих. Коэффициент потери обычно составляет 4%-16%. Коэффициент потери для импортного шпона составляет 2%-11%.
5) Горячее прессование
После проклейки, шпоны склеиваются в случае определенной температуры и давления. С изменением температуры заготовки и влажности, шпон сокращается. Потеря данной секции связана с температурой, давлением, временем прессования, материалом, влажностью и т.д. Коэффициент потери обычно составляет 3%-8%.
6) Обрезка краев
После секции горячего прессования, заготовка вырезана в качественную фанеру. Остатки связаны с припуском обработки и размером продукции. Чем больше размера продукта, чем меньше отходов. Коэффициент потери обычно составляет 6%-9%.
7) Шлифовка
Шлифовка делает фанеру чистым. Потеря данной секции – порошок для шлифовки. Чем лучше качества шпона, тем меньше порошка. Коэффициент потери обычно составляет 2%-6%.
8) Складирование
Упаковка на поддонах или без упаковки
Основные особенности оборудования для производства фанеры
1. Автоматическая подача доски
2. Точное позиционирование доски
3. Экономия сырья.
4. Высокая эффективность формовки.
5. Стабильное рабочее состояние
6. Длительный срок службы
7. Автоматическая гидравлическая система
8. Автоматическое управление
Другие названия: Машина для производства столярных плит, линия для производства столярных плит, горячий пресс для склеивания фанеры
-
- Производственная линия по выпуску МДФ (Оборудование для производства древесно-волокнистой плиты средней плотности)С широким применением, МДФ (Древесно-волокнистая плита средней плотности) является отличной заменой натуральной древесины. Она широко используется для мебели, при ...